Сыну напечатал игрушку, а станции - задвижку
22.04.2021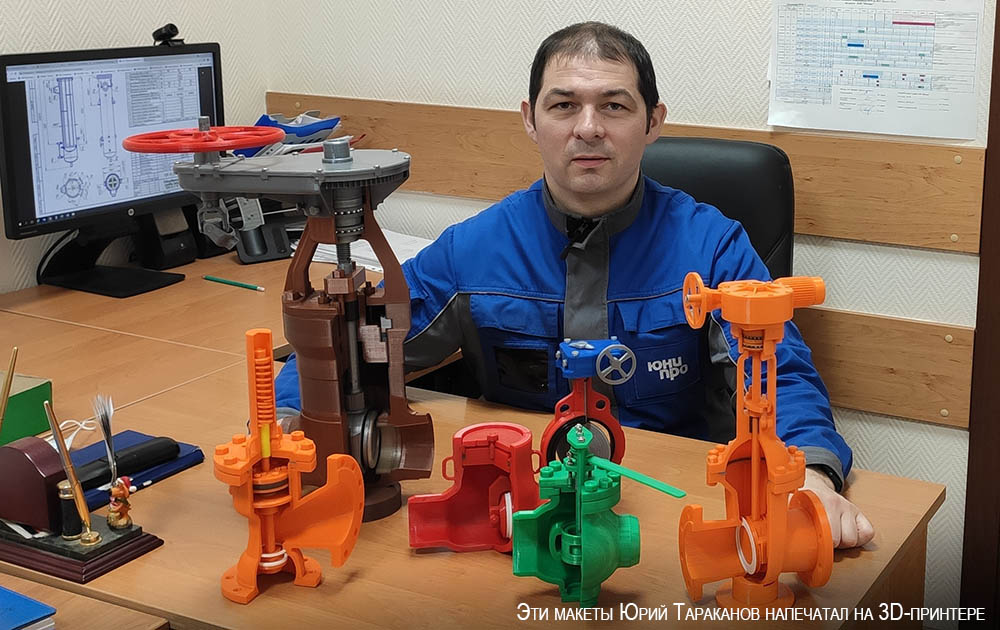
Аддитивное производство, оно же – трехмерная печать, с каждым днем становится только популярнее. Сегодня 3D-принтеры используются как в личных целях, так и для производственных нужд. Современное увлечение не обошло стороной и старшего мастера цеха централизованного ремонта Сургутской ГРЭС-2 Юрия Тараканова. Его можно даже назвать пионером внедрения 3D-печати в работу энергообъекта.
Приучай к 3D смолоду
История серьезного увлечения Юрия аддитивными технологиями началась осенью 2020 года, в разгар пандемии. Незадолго до этого он приобрел 3D-принтер для печати из пластика, чтобы занять 11-летнего сына. Мальчик увлекается робототехникой, интересуется техникой в целом, а потому подарок принял на ура. И так вышло, что вместе с ребенком папа и сам стал поклонником современной технологии.
«Начал с производства самых простых игрушек и брелоков, – рассказывает Юрий. – Но постепенно осваивал 3D-печать и создавал все более интересные изделия. Чтобы что-то напечатать, нужно создать 3D-модель этого объекта на компьютере ну или просто найти ее в Интернете. Я немного владел программой «Компас 3D» для трехмерного моделирования, и это мне очень пригодилось. Кстати, сама печать одного достаточно несложного изделия может длиться от 20 минут до 10–20 часов.
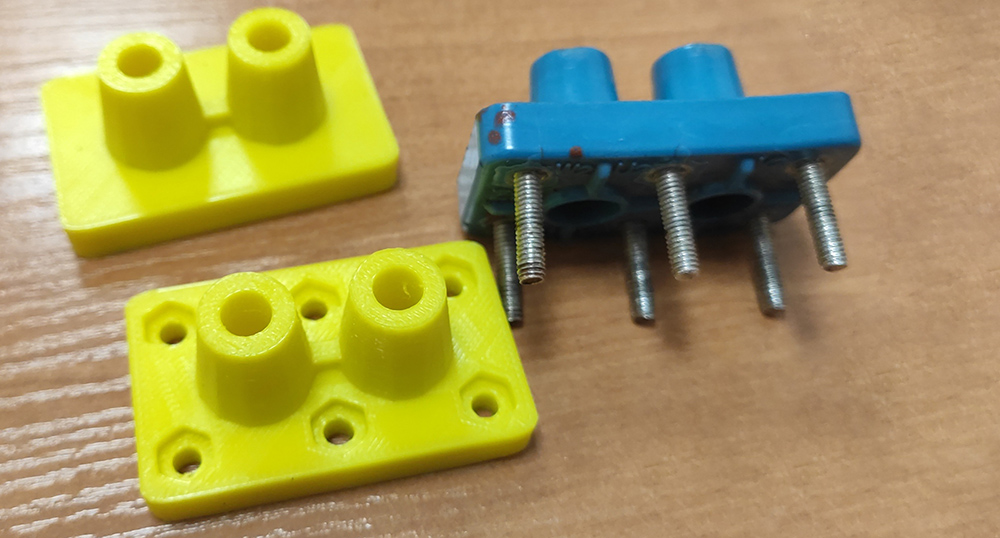
Энергетикам в помощь
Вскоре Юрий решил, что аддитивные технологии могут послужить и на благо Сургутской ГРЭС-2. На своем 3D-принтере он создал несколько учебных моделей в образовательных целях: задвижки – клиновая ручная и высокого давления, клапаны – регулирующий поворотный, предохранительный, обратный. Напечатал также несколько запчастей для электроприводов арматуры, их сегодня применяют в своей работе сотрудники станции. Сейчас своей очереди ждут чертежи арматуры высокого давления, Юрию прислали их с завода – производителя такого рода изделий. Наш герой планирует вскоре начать печать и признается, что принтеру предстоит очень трудоемкая работа.
«3D-печать пластиковых изделий сегодня перестала быть дорогим удовольствием, – отмечает Юрий. – Принтер можно купить за 15 тысяч рублей, килограмм пластика в виде нитки в катушках – около 1 тысячи рублей. На изготовление макета задвижки или клапана расходуется порядка 500–600 граммов. К слову, есть еще принтеры, работающие с порошком для печати металлических изделий, но это пока еще дорогая технология. В целом я уверен, что аддитивное производство – это очень перспективное решение. Таким образом сегодня создаются даже лопатки для газовых турбин. 3D-печать активно используют во всем мире, и думаю, что со временем она будет все более дешевой и массовой».
— Сегодня макеты, изготовленные на 3D-принтере, позволяют обучать персонал ряда цехов работе с разными типами арматуры, наглядно демонстрировать элементы, которые подвержены частым поломкам. В целом это поможет нам сократить количество таких поломок и ускорить процессы ремонта арматуры. В перспективе использование 3D-печати способно принести огромную пользу не только в учебных, но и производственных целях. Например, можно сократить время проведения ремонтов за счет оперативного изготовления пластиковых деталей. Некоторые такие запчасти сегодня приходится долго искать, заказывать и ждать поставку. Или, например, на изготовление традиционным методом втулки электропривода арматуры из металла требуется 14,5 часа. Необходимо привлечь для выполнения операции трех специалистов механического участка. Чтобы изготовить такой же элемент из пластика на 3D-принтере, понадобится: 5 минут на подготовку и 5 часов самой работы принтера. Участие человека при печати не требуется.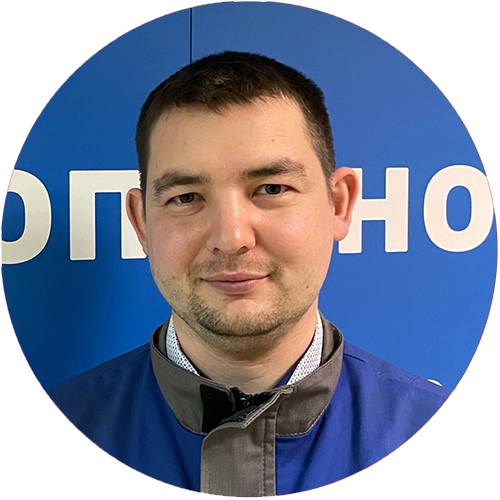
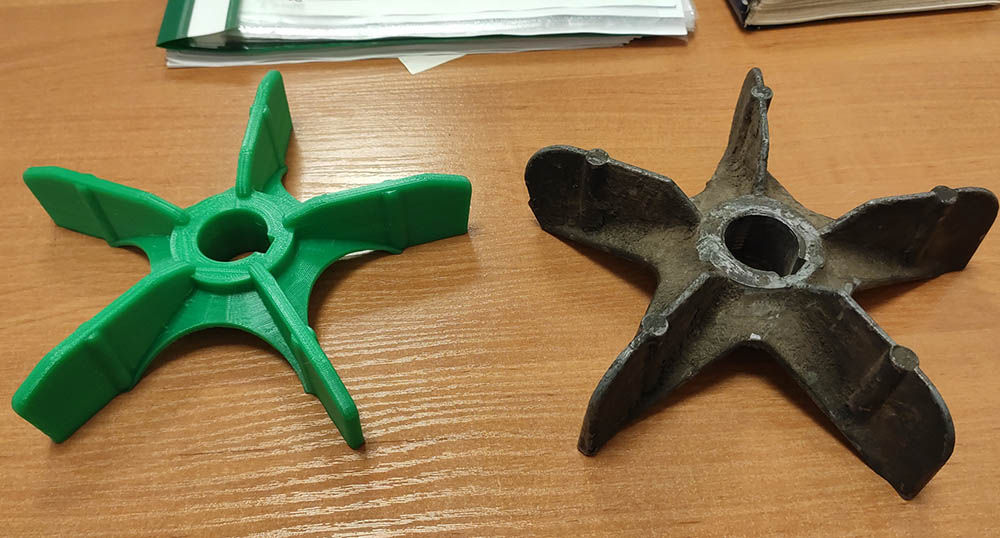
Путь инноваций
К слову, не только аддитивные, но и другие современные технологии в скором времени смогут найти свое место на Сургутской ГРЭС-2. Например, планируется взять на вооружение лазерную очистку металлических поверхностей и использование лазерного станка для гравировки и резки изделий небольшого размера. Станок для гравировки и резки даст возможность, например, самостоятельно изготавливать таблички с диспетчерским наименованием оборудования.
— Современные технологии могут упростить и ускорить процесс ремонта. Речь идет о лазерной очистке ремонтируемых деталей от различных отложений. Материал при поглощении энергии от излучения лазера быстро нагревается, что приводит к испарению. При этом поверхность, расположенная ниже, не подвергается воздействию – не нарушается структура и поверхность обрабатываемого элемента. Такой метод очистки отличается от применяемого сейчас в 10 раз в плане быстроты. В скором времени состоятся испытания лазерной очистки на площадке одного из отечественных производителей. Образцы для очистки будут предоставлены с другой станции Юнипро – Шатурской ГРЭС.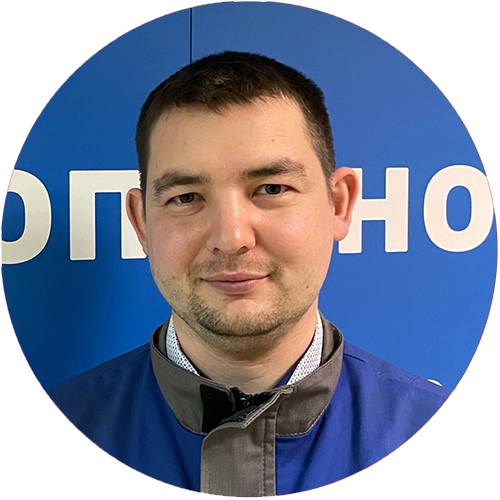
Поделиться
Читайте также
Лазер в руки!
На Березовской ГРЭС осваивают систему лазерной центровки.
Готовы к ОЗП
ПАО «Юнипро» получило паспорт готовности к осенне-зимнему периоду (ОЗП) 2023‑2024 года.
«Всем бы таких начальников!»
Ветеран Шатурской ГРЭС Виктор Иванович Гаврюшин посвятил энергетике всю жизнь. Его общий трудовой стаж составляет 57 лет, из которых 26 он отработал на родной станции.
Учимся беречь энергию
Сотрудники Смоленской ГРЭС провели уроки энергосбережения для школьников.
Комментарии
Чтобы оставить комментарий авторизуйтесь