Найти то, что тоньше волоса
10.03.2025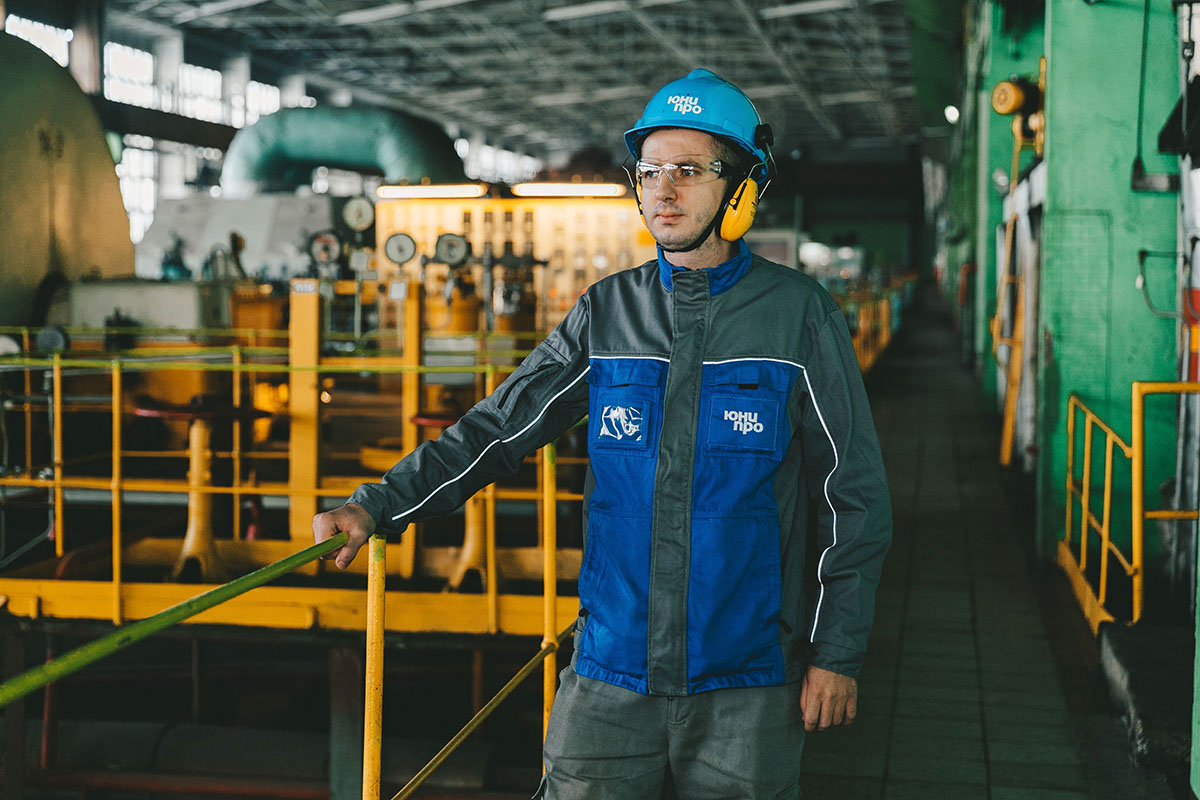
В этом заключается кропотливая работа дефектоскопистов на станциях Юнипро.
Представители этой специальности выявляют дефекты, которые не видны снаружи. Задача непростая и очень ответственная: ведь на таком объекте, как электростанция, каждый пропущенный дефект может обернуться аварией. Артем Доронин, дефектоскопист по магнитному и ультразвуковому контролю Шатурской ГРЭС, уже 10 лет занимается выявлением скрытых нарушений в металле оборудования, трубопроводов и сварных соединений. О секретах своей профессии он рассказал «Юнипро Мегаватт».
Постоянный контроль
Оборудование на тепловой электростанции должно находиться под постоянным контролем: для энергетиков это правило крепче железа. Кстати, как раз железо на станциях и работает с самыми большими нагрузками: высокая температура и высокое давление горячей воды и пара, вибрация способны постепенно расшатывать любое соединение... Металл «устает», и нужно время от времени проверять, не готов ли он дать слабину и прорваться? Даже незаметная глазу трещина или скрытый в сварном шве непроваренный участок могут привести к серьезному сбою, остановке работы энергоблока. И хорошо еще, если без тяжелых последствий…
Так что контроль, контроль и еще раз контроль.
Входной контроль: все поступающее на станцию оборудование обязательно проверяется на соответствие качества материала, проводится множество исследований, определяется химический состав металла и его твердость, толщина, идет поиск скрытых дефектов.
Плановый, эксплуатационный контроль: проработавшее какое-то время (для каждого изделия — свое) оборудование обследуют и опять же ищут дефекты — на этот раз вскрывшиеся, образовавшиеся в слабых местах.
Ремонт или замена: каждое место сварки обязательно нужно тщательно проверить, подтвердить, что шов действительно готов выдержать необходимую нагрузку.
Вся эта постоянная кропотливая работа ложится на плечи отдела технической диагностики (ОТД) и тех, кто ищет и выявляет дефекты – дефектоскопистов.
«Утром мы получаем сменное задание от начальника ОТД, определяем, какие потребуются методы контроля, – рассказывает Артем Доронин. – После этого берем соответствующее оборудование, настраиваем его и отправляемся на рабочее место, где проводим сам контроль. О его результатах докладываем начальнику отдела. По ним и по выявленным дефектам делаем заключение в электронном виде». С виду работа как работа, если не учитывать, например, сколько высокотехнологичных методов контроля используют дефектоскописты Шатурской ГРЭС.
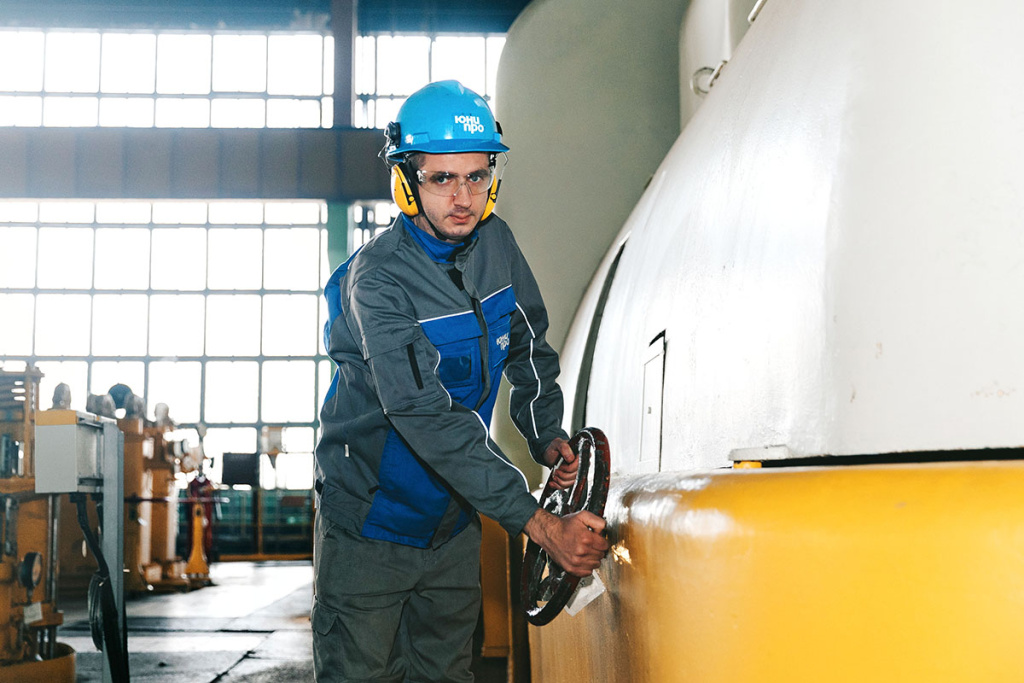
УЗИ стальной трубы
Что такое УЗИ — ультразвуковое исследование — в наше время представляет себе, наверное, любой взрослый человек: в поликлиниках такой метод диагностики давно стал обычным и привычным. Человека вместо рентгеновских лучей «просвечивают» направленным ультразвуковым пучком, и врач на мониторе сразу может определить состояние внутренних органов или, например, пол будущего ребенка. С ультразвуковым контролем металлических изделий все обстоит точно так же. Разве что в роли пациента здесь выступают трубы или сварные швы, а диагноз им ставит не врач, а дефектоскопист. И еще к врачу пациенты приходят сами, а дефектоскописту приходится забираться в любой уголок станции: котел или бак в кабинет УЗИ не поместятся!
«У нас сейчас приборы удобные, компактные, – говорит Артем Доронин. – Кладем их в сумку и идем на место проведения контроля. Можем добраться практически до любого шва. Где работают сварщики, там и мы проводим свой контроль – подтверждаем качество выполненного нашими коллегами ремонта».
Ультразвук позволяет выявить не только непровар или пористость сварного шва, но и дефекты, образовавшиеся в основном металле. Появилась ли раковина, расслоился или истончился металл в каком-то месте – все это можно увидеть и рассчитать, сколько еще может прослужить эта деталь, через какой срок потребуется ее замена.
Для трещин в металле, которые невозможно обнаружить невооруженным глазом, потому что они тоньше человеческого волоса, существует магнитопорошковая дефектоскопия – МПД.
«Вот перед нами деталь. Ее зачистили до блеска, на ней вроде бы ничего нет, – делится секретами профессии наш собеседник. – Но мы подключаем к ней магнитопорошковый дефектоскоп – прибор, который будет создавать на поверхности детали электромагнитное поле, и наносим специальную суспензию, в которой разведен порошок из очень мелких магнитных частиц. Если есть трещина, на ее кромках частицы порошка собираются вдоль кромок. Любая, самая мелкая трещина сразу проявляется, можно увидеть ее форму и размер, обозначить контур. Причем все это происходит очень быстро, и можно сразу обследовать большую поверхность».
А как быть с деталями из цветных металлов или немагнитной нержавеющей стали? Здесь на помощь приходит другой метод – цветная дефектоскопия. На очищенную и обезжиренную поверхность детали наносят специальный состав – пенетрант, который глубоко проникает в мельчайшие поры и трещины. Когда жидкость впитается, деталь промывают водой, потом просушивают горячим воздухом и наносят белый проявитель. На высохшем слое проявителя станет заметен рисунок трещин: краска пенетранта из них вытягивается на белый фон проявителя. Чем шире и ярче цветная линия, тем больше в нее впиталось пенетранта, а значит, тем глубже под ней трещина.
Ну, а для определения химического состава металла используется метод рентгенофлуоресцентного анализа. Небольшой анализатор облучает деталь рентгеновскими лучами, и на экране прибора сразу высвечивается, какие и в каком количестве в этой стали присутствуют легирующие элементы. Цена такого суперсовременного оборудования весьма немалая, но надежность и безопасность работы станции всегда дороже!
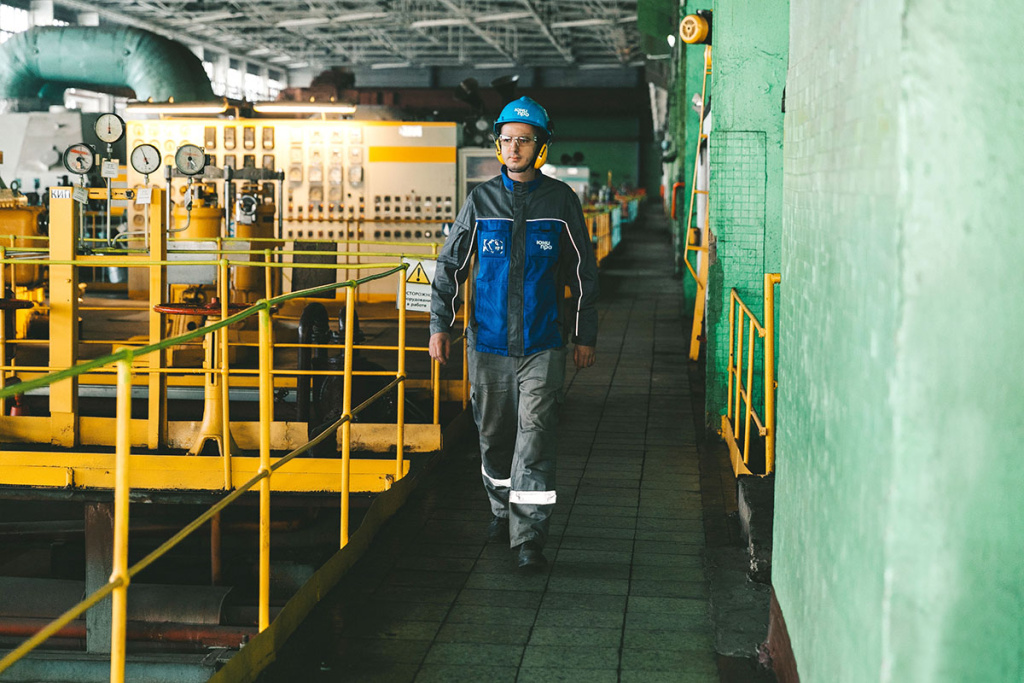
Дефект найден, а что потом?
Шатурская ГРЭС – станция весьма солидного возраста, и старым оборудованием на ней никого не удивишь. А значит, и возрастные «болезни» металлических изделий обнаруживаются часто: несколько раз в неделю Артем Доронин и его коллеги находят тот или иной дефект. И даже если выявленная проблема не грозит аварией в ближайшее время (например, стенка трубопровода стала тоньше, но нагрузку еще выдерживает), дефектоскописты обязательно оформляют и предоставляют руководству заключение с подробным описанием найденных отклонений от заданных параметров. Дальше по проблемному участку будет приниматься решение: заменять или ремонтировать оборудование, делать это прямо сейчас или можно подождать до планового ремонта.
«Обычно мы находим все-таки небольшие дефекты, с которыми деталь вполне может проработать еще полгода или год, – поясняет Артем Доронин. – Но потом при первой же остановке этого узла замену нужно произвести обязательно, так что дефектный участок включается в план ремонта. И каждый раз мы должны очень тщательно провести обследование, уточнить степень риска по обнаруженной проблеме, ведь на нас лежит большая ответственность. Если вовремя не обнаружить дефект или недооценить риск, может произойти авария с остановкой оборудования, отклонение от заданного диспетчерского графика. Но если мы выявили крупный дефект, нужно срочно его устранять, ремонтировать, так как под угрозой оказывается не только работоспособность оборудования, но и здоровье, и даже жизнь наших сотрудников!»
Любую проблему лучше предотвращать заранее, чем устранять последствия, поэтому еще одним важнейшим направлением работы дефектоскопистов является входной контроль. Нового оборудования сейчас на станцию поступает много, и здесь тоже время от времени выявляется брак в работе изготовителей. Рентгеновский анализатор в руках Артема видит все: и несоответствие химического состава стали заявленной марке, и «не тот» металл, наплавленный в сварном соединении. Недостаточная толщина, выявление дефектов в металле – и забракованное изделие отправляется обратно на завод для устранения того, что пропустил ОТК изготовителя, но обнаружил на станции бдительный ОТД и его дефектоскописты – профессионалы, использующие в своей работе самые современные методы.
— Да, наша работа требует очень много усилий, знаний, внимания, но этим она мне и нравится! – признается Артем Доронин. – Это большая ответственность, но и ощущение того, что делаешь что-то по-настоящему важное, и для всех людей, с которыми работаешь на станции, и, по большому счету, для всей страны. А еще у нас бывает много командировок в разные города России, а это всегда новые места, возможность познакомиться с интересными людьми, нашими коллегами, возможность получить новые впечатления, да и просто сменить обстановку. Так что скучать у нас не приходится!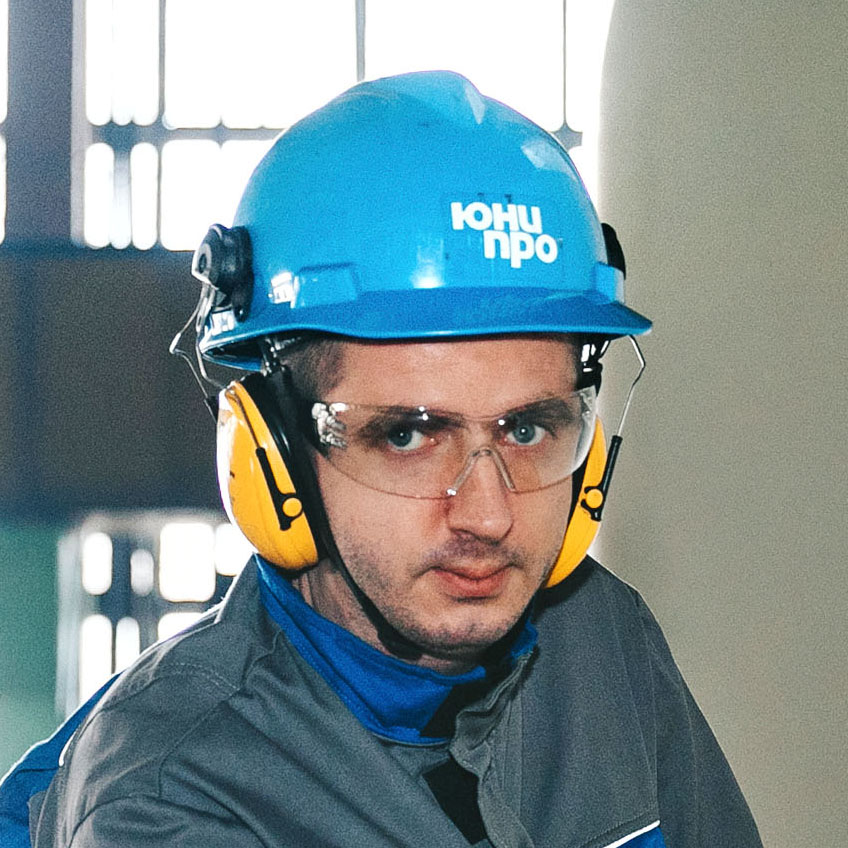
Поделиться
Читайте также
Управление спросом на электроэнергию: зачем это нужно
В России развивается новый рыночный механизм.
На большом плоту по Мане
Сотрудники Березовской ГРЭС совершили незабываемое таежное путешествие.
Рожденный на болотах
Шатурская ГРЭС дала жизнь примечательному поселку.
А вот теперь садись и слушай
Сто лет назад на шатурской земле появилось радио.
Комментарии
Чтобы оставить комментарий авторизуйтесь